The thermoplastic paint production equipment currently produced by our company can realize automated continuous production, and the output requirements can be met from 1t/h to 30t/h and can be customized according to your needs.
Introduction to the thermoplastic paint production process
Basic composition of thermoplastic paint
The basic ingredients of thermoplastic paint are resin, pigment, solvent, and additives.
The manufacturing process of thermoplastic paint
Pre-dispersion --- grinding --- mixing adjustment --- color adjustment --- testing - filtering and packaging.
The thermoplastic paint equipment
High-speed disperser
Dispersers can mix the pigment with part of the paint and turn it into a semi-finished product of pigment paste. It is the first process in paint production.
Purpose:
- Make the pigments mix evenly;
- Make the pigments partially moist;
- Preliminarily break up large pigment aggregates.
It is mainly mixed and partly dispersed to prepare for the next grinding process.
The good or bad effect of dispersion directly affects the quality and efficiency of grinding and dispersion. The main equipment used is a high-speed disperser.
High-speed disperser is not only used as dispersing equipment but also can be used as coating production equipment. For example, if the pigment of the coating is easy to be dispersed, or the fineness of the color paint is not high, then, it can be directly dispersed by a high-speed disperser to produce coatings.
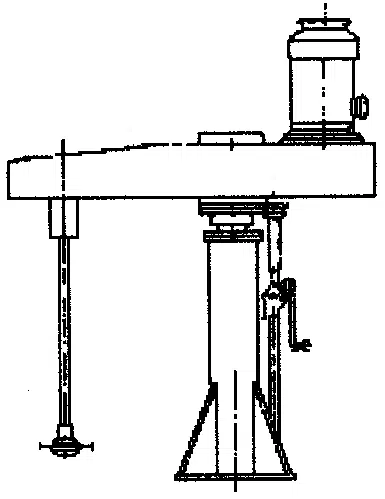
Its structure is shown in the picture (for floor-type high-speed disperser) and consists of a machine body, transmission device, spindle, and impeller.
The machine body is equipped with hydraulic lifting and slewing device, the hydraulic lifting is provided by gear oil pump to provide pressure oil to make the head rise and fall by its weight, and the descending speed is controlled by the stroke throttle valve. Slewing device can make the machine head rotate 360 °, after the rotation of the handle locking positioning. The transmission device is driven by the motor through the V-belt, and the motor supports customization, or the belt step-less speed regulation, frequency conversion speed regulation, and so on.
The key component of the high-speed disperser is the serrated disc impeller, as shown as the following picture.
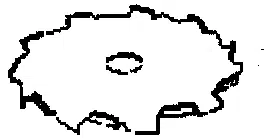
There is a direct relationship between the impeller diameter and the size of the mixing tank, empirical data show that the mixing tank diameter by φ = 2.8-4.0D (D: impeller diameter), is the most ideal dispersion effect.
The high-speed rotation of the impeller makes the paint slurry present a rolling circulation, and produces a large vortex. At the edge of the impeller 2.5-5cm, a turbulence zone is formed, in which the pigment particles are subjected to strong shear and impact effects, which make them quickly dispersed into the paint slurry.
When the rotating speed of the impeller reaches about 20m/s with the circumferential speed of the impeller, a satisfactory dispersing effect can be obtained. If the speed is too high, it will cause the paint to splash and increase the power consumption.Vmax=20--30m/s.
The installation of the high-speed disperser is divided into: floor type, suitable for pulling cylinder operation, and the other one is installed on the rack, one disperser can be used for several fixed tanks.
Grinding and Dispersing Equipment
Grinding equipment is the main equipment for the production of thermoplastic paints, the basic type is divided into two categories, one with grinding media, such as sand mills, or ball mills, and the other type that does not have grinding media and relies on wiping force for dispersion, such as three-roller machine, single-roller machine.
Equipment with grinding media relies on grinding media (such as glass beads, steel beads, pebbles, etc.) in the impact and rolling or sliding each other when the impact and shear force for grinding and dispersion. It is usually used in the production of medium and low-viscosity paint slurry with good fluidity, large output, and high dispersing efficiency. Grinding and dispersing equipment without grinding media can be used for the production of very high viscosity and even paste-like materials, like sand mill machines.
Vertical sand mill
Its external structure is shown in following picture, which consists of machine body, main motor, transmission parts, cylinder, disperser, feeding system and electrical manipulation system.
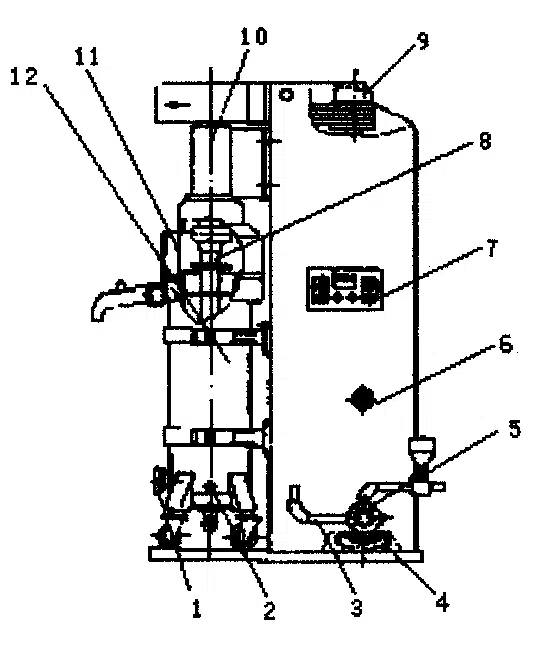
Vertical sand mill machine structure sketch:
1-Discharge and sand release port; 2-Cooling water inlet; 3-Feeding pipe; 4-Stepless speed changer; 5-Feeding pump; 6-Speed control handwheel; 7 Manipulating button plate; 8-disperser; 9-centrifugal clutch; 10-bearing housing; 11-screen; 12-simplified body.
Working principle: the pre-dispersed paint slurry by the feed pump from the bottom of the input, the flow rate can be adjusted, the bottom valve 8 is a special one-way valve, can prevent the pump stop after the glass beads backflow. When the paint is fed, start the sand mill, the dispersing shaft drives the dispersing disk 5 high-speed rotation, the dispersing disk outer edge of the circumferential speed of about 10m / s (dispersing shaft speed between 600-1500 rpm). Near the dispersing disk around the paint and glass beads by the viscosity resistance with the dispersing disk running, thrown to the cylinder wall of the sand mill, and then return to the center, the pigment particles are therefore subjected to shear and impact, dispersed in the paint. The dispersed paint slurry overflows from the outlet through the screen, and the glass beads are intercepted by the screen.
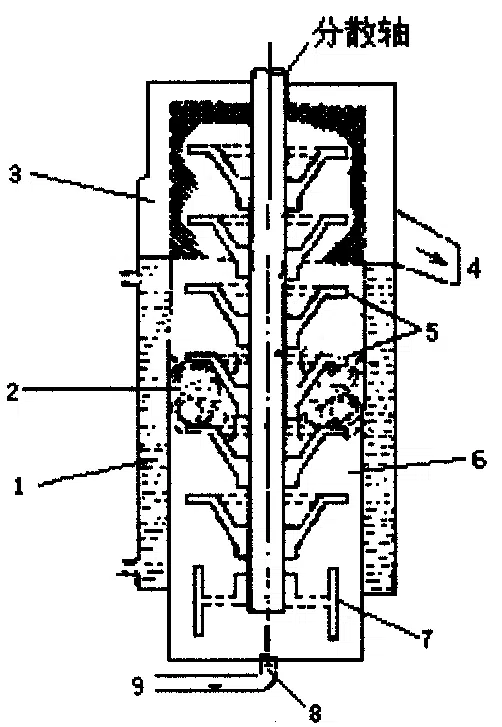
Conventional sand mill machine principle schematic diagram:
1-water jacket; 2-typical flow pattern of slurry sandwiched between two dispersing disks (double circular rolling grinding action); 3-screen; 4-dispersed slurry outlet; 5-dispersing disks: 6-mixture of slurry and grinding media; 7 - Balancing wheel; 8 - Bottom valve; 9 - Inlet for pre-mixed slurry.
- The paint slurry still can't reach the fineness requirement after dispersing once, it can be ground again by sand mill until qualified.
- Several (2-5) sand mill machines can also be used in series. The use of sand grinding up to 20μm or so.
- Glass beads diameter 1-3mm, due to wear and tear should be frequently cleaned, sifted, and supplemented.
- Sand mill machines in the operation process, due to friction will produce a large amount of heat, so the machine outside the barrel body is made of jacket type, through the cooling water cooling.
- Laboratory sand mill machine is generally <5L, production sand mill for 40-80L, is the effective volume of the cylinder to measure the above values, its production capacity like 40L sand mill machine can generally process 270-700Kg of color paste per hour.
When using the sand mill machine, you should pay attention to:
- It is strictly forbidden to start when there is no material and grinding media in the cylinder, otherwise, the dispersion disk and glass beads will be severely worn.
- When driving, you should start the feeding pump first, and then start the main motor after the paint slurry is seen at the discharge port.
- After parking for a long time, you should check whether the dispersion disk is stuck and do not start it by force.
- After parking for a long time, check whether the top screen is dry and crusted to prevent paint slurry from overflowing from the top screen after driving (roof collapse).
- When cleaning and sanding, the high-speed disperser can only be moved in a jog to reduce the wear of the dispersing disc and grinding media.
- When using new grinding media, it should first be screened to remove impurities.
Thermoplastic paint mixing equipment
In addition to the high-speed disperser mentioned earlier can be used to mix the paint color, and mass production, generally using the paint mixing tank, which is also commonly known as the color mixing cylinder. The paint mixing tank is installed on the shelf above the ground, its structure is relatively simple, see the following picture, by the mixing device, and drive motor, the mixing tank consists of several parts. Stirring paddle can be installed at the bottom and side, the motor can be single-speed or multi-speed.
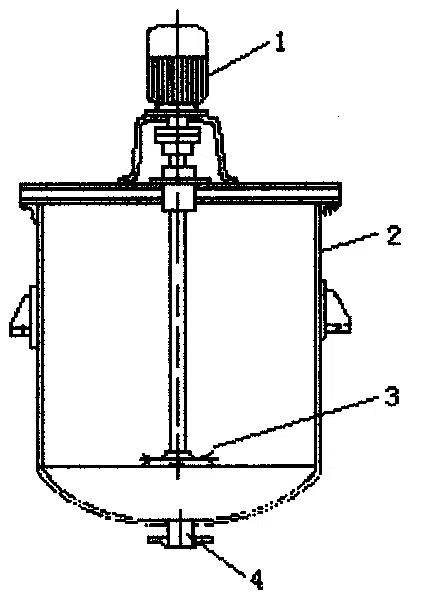
High-speed paint mixing tank with direct electric motor connection:
1 - drive motor; 2 - mixing tank; 3 - sawtooth disc paddle; 4 - discharge port.
Filtration equipment
Paint in the production process will inevitably be mixed with flying dust, impurities, sometimes produce paint skin, in the factory before packaging, must be filtered. Commonly used for color paint filtration equipment are Luo screen, filter press, vibrating screen, bag filter, tube filter and self-cleaning filter.
- Luo sieve
In a Luo ring taut on the appropriate specifications of copper wire mesh or nylon silk, it will be placed in the iron or stainless steel funnel, is a simple filter with Luo sieve. - Vibrating sieve
The screen is vibrated at high frequency, which can avoid the filter residue blocking the sieve holes. - Filter press machine
Commonly known as multi-face Luo. In a cylindrical simple body with a fast-opening lid, suspended a filter cylinder covered with small holes, in the filter cylinder covered with metal wire mesh or silk cloth, the filtered paint is pumped into the upper part of the filter, into the mesh basket, the impurities are retained, the filtrate from the bottom of the filter outflow. - Bag filter
Commonly used equipment for paint filtration, the filter bag is installed in the slender body with metal mesh bag for support. When working, it relies on the pump to send the paint into the bag, the filter residue stays in the bag, and the qualified paint slurry flows out from the outlet. Bag filter generally equipped with a pressure gauge, operation, when the pressure rises, filtration resistance increases, when it reaches 0.4Mpa, it should be shut down, replace the filter bag.
The filter should be cleaned at any time after each use to keep it neat and tidy for the next use.