[lwptoc skipHeadingLevel="h1,h4,h5,h6"]
How to calculate cement silo capacity?
How to calculate cement silo capacity?
1. the production capacity of your mixer, how many cubic meters of concrete can be produced per hour, and how much cement do you need to use per cubic meter of concrete? Generally speaking, the amount of cement is usually between 250~350kg; you can calculate the cement silo capacity to be 300kg.
2. The supply of cement silo, if it is bulk cement, you need to consider whether the collection of cement is timely; if it is bagged cement, then there should be a big cement warehouse near the concrete batching machine; you need to consider in what way the cement is delivered to the cement silo and whether it is affected by the weather.
3. If your cement silo is full of cement, how many hours of continuous operation can the mixing plant be guaranteed? Some say that one cement tank can ensure the concrete batching machine works continuously for 2 hours. According to the domestic situation and my experience, the cement silo capacity should not be less than the cement required for one shift of the mixing plant. Otherwise, it may affect the continuous operation. For example: For a 40m3/h concrete batching machine, the minimum capacity of the cement silo is 40 × 0.8 × 300 /1000 × 8 = 77t. The 0.8 in the formula is the ratio of the actual capacity to the nameplate capacity.
How many cement silos do you need?
A concrete batching plant must have one or more cement silos to reserve a certain amount of cement delivered to the concrete mixer at any time in a certain ratio. So how many cement silos are needed? It depends mainly on how many types of cement and additives you have available.
Cement silo parts
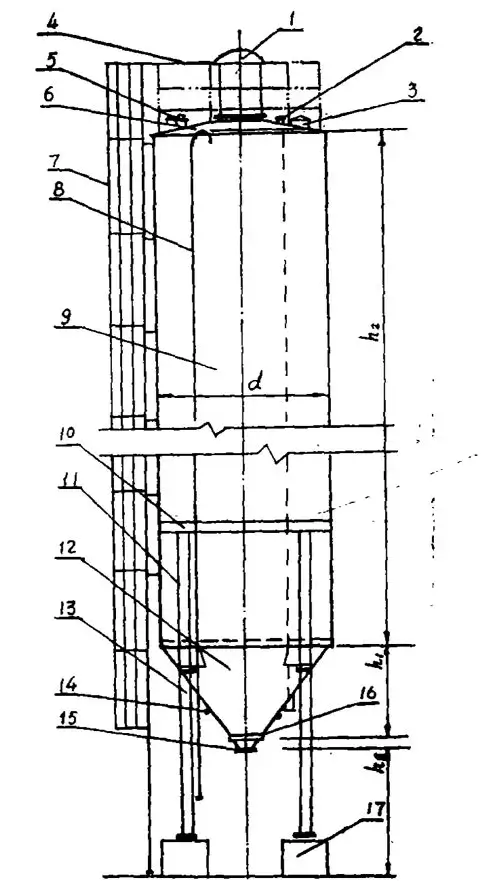
1. Dust collector
2. Material level meter and joint
3. Access hole
4. Top guard rail
5. Safety valve
6. Bin roof cover
7. Climbing ladder
8. Into the cement pipe
9. Cement silo body
10. Strengthening hoop
11. Side support
12. Cone bottom of silo
13. Cement silo support
14. Arch breaking device
15. Cement silo support
16. Cement discharge valve
17. Rainproof plate
18. Foundation
Cement silo dust collector
No matter if it is in bulk or bagged; currently, most of the cement is transported by wind power. The input of cement to remove air requires the use of cement silo dust collectors.
Nowadays, a bag filter is commonly used. The air with cement dust passes through the cloth bag of the dust collector, and the air passes through the cloth bag to keep the cement dust on the bag cloth. The cement silo dust collector periodically vibrates the bag so that the cement falls into the cement bin, thus maintaining the ventilation performance of the bag.
The filtering air speed of the bag cloth is less than or equal to 1m/s ~ 2m/s. With high-pressure air to transport cement into the silo, the air volume is <9m3/min. With low pressure, the air is about 15m3 /min. So the area of 14 square meters is enough for the bag filter.
If the cement is transported into the warehouse by high-pressure wind, the cement silo dust collector can be without the induced draft fan; the remaining pressure is enough to pass the filter bag; if the low-pressure wind is used, it is better to bring the induced draft fan to exhaust, which also helps the wind transport. Because the bag-type dust collector is installed at the top of the cement silo, it is subject to the greatest wind and is often wet by rain. Therefore, the shape of this dust collector is preferably barrel-shaped to reduce the wind force and must be rainproof.
Gravity Safety Valve
Nowadays, the cement used in the concrete batching plants is mostly bulk, and the air pressure of bulk cement trucks conveying cement is 0.2~3.0MPa, which is enough for the bin with a 3m diameter. For cement silo safe, a gravity safety valve is installed on the top of the silo, and the opening pressure of the safety valve is set at 0.05MPa.
Cement silo level sensor
The cement silo level sensor indicates the amount of cement stored in the silo and will alarm at the highest or lowest limit. It provides the concrete batching machine operator with the necessary data to arrange the operation plan.
There are two types of cement silo level sensors: one can only alarm at the highest or lowest level; it is an electrical type. The other is the capacitive type, which can indicate the cement level from 0 to 100%, but not the absolute value.
Cement silo valve
There are two kinds of cement silo valves: one is a pull plate valve, and one is a butterfly valve. The former is complicated to process and often prone to failure, so the butterfly valve is generally used in concrete silos.
Arch breaking device
If the cement produces arch plugging, the arch needs to be broken by wind power. In other words, three or four air nozzles are evenly distributed along the circumference of the bottom cone near the discharge port, and the arch is broken by compressed air spray. Here to raise attention, the compressed air used must be condensate and oil separated to remove so as not to make the cement deteriorate.
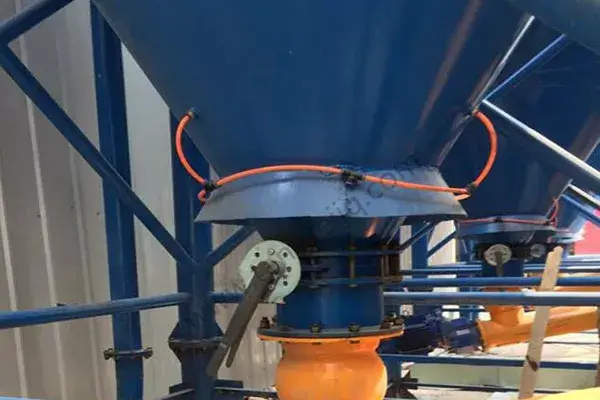
How do we determine the cement silo size of each part?
Before calculating the strength of each part of the cement silo, the following main dimensions must be determined first.
The diameter of the cement silo body
The diameter of a cement silo is mainly restricted by the transportation conditions, such as the limits of railroad vehicles, buildings, loading, bridges, and tunnels; Therefore, the diameter of the cement silo is less than or equal to 3 m. Of course, if you have a sheet cement silo, you do not need to consider this problem.
The diameter of the cement silo discharge port
The bottom cone of the cement silo of the concrete mixing plant is generally conical, then the formula to calculate the discharge capacity of the cement silo is:
Q= 3600V- A-Y (t/h)
V= cement flow rate n /s; A= vertical passing area m2; Y= cement capacity 1.45t/m 3
How do we determine the discharge capacity of a cement silo?
If a 60m3/h concrete mixing plant is set, it takes the 60s to produce a batch of concrete. The production of a concrete batch includes the input of various mix components (sand, stone, cement, water, additives, etc.) and the mixing and discharging of concrete, which overlaps in time. But the cement weighing hopper into the cement and unloading cement to the mixer must be separate, such as into the mixer for 10s, plus the screw conveyor start and stop time for 2S. In the cycle, the rest of the time, 60-12 = 48S is the longest time the screw conveyor to the cement weighing hopper sends cement. In addition, the mix ratio can not be calculated by the average 300kg/m3; it should be the highest amount of cement, 350kg/m3, to check the calculation.
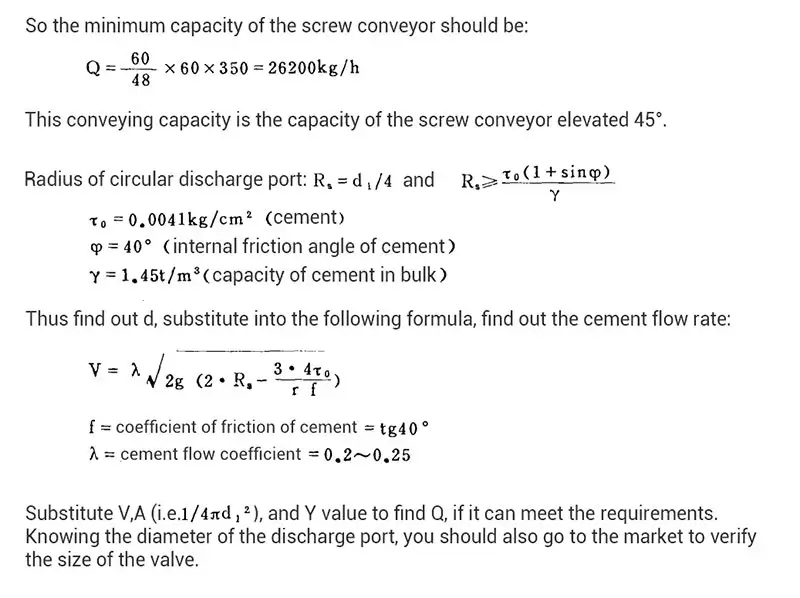
The height of the cement silo bottom cone
To facilitate the smooth flow of cement out of the cement silo, the angle of the cement silo bottom cone will be 54 ° ~ 60 ° because of the impact of friction between the cement and steel plate; the maximum cone angle of the cement bin is 80°, then the height and volume of the bottom cone of the cement silo will be found.
The distance of the cement silo discharge port from the ground.
A cement silo discharge port will be installed at the discharge gate plate valve or butterfly valve because it is not often operated; the manual type is generally used, that is, the manual butterfly valve. The height of the centre of the valve is more suitable, below 1.8m, too high for easy operation. If it is too low, the centre of gravity of the cement silo is certainly lowered, the elevation angle of the screw conveyor is too large, and the conveying efficiency is reduced. The angle of the screw conveyor is generally between 25° and 35°, not more than 45°.
How do I deliver cement to a cement silo?
There are both mechanical and wind-powered methods of conveying cement into cement silos. The mechanical type includes chain bucket elevator and screw conveyor, mostly used for bagged cement.
The cement wind conveying system is divided into high-pressure and low-pressure wind types. Mostly used for bulk cement, the conveying truck is equipped with an air compressor, and the wind pressure is 0.2~0.3 MPa. The cement silo has a feeding pipe and can be connected with a bulk cement conveying truck by hose. In low-pressure wind conveying equipment, the wind pressure is 0.05 MPa to reduce resistance, generally into the cement pipe diameter of 100 ~ 125.
Top of cement silo
The cement silo top is equipped with some accessories, and a 1:1 ramp is usually adopted to prevent water from soaking into the silo and facilitate drainage.
The bearing force of cement silo
Here the strength calculation of each part of the cement silo is not introduced in detail, but only some analysis of the bearing force of the cement silo is made.
The static load of cement silo
The static load is the self-weight of cement silo and accessories, which includes:
- Cement silo roof plate and its accessories, such as dust collector, safety valve, etc.
- Cement silo barrel and its inlet pipe and bracket.
- Handrails and ladders on the cement silo roof plate.
- Reinforcement parts of cement silo barrel.
- Cement bin bottom cone.
- Bracket and supporting parts.
- Discharge port valve and part of the weight of screw conveyor.
Variable load
The cement in the silo changes at any time and should be filled with cement according to its maximum volume-weight, i.e. the part below the inlet pipe. The key data here is the volume-weight of cement. Because the cement silo barrel is high, the cement is compacted, and its volume-weight is 1.6~1.7t /m 3 more appropriate.
Horizontal load
There are two kinds of horizontal loads on cement silos: one is wind, and the other is an earthquake. These two kinds of forces should be treated with caution. Otherwise, it may lead to adverse consequences. If your cement silo is built in a coastal area, you need to explain to the cement silo supplier to customize the cement silo.
If the design is not specified before the use of the site, the wind and earthquake levels are not clearly defined; for the safety of cement silos:
- Wind speed: 150~~200km / h
- Seismic intensity: 9
- Seismic coefficient: 0.05~0.10, preferably 0.07~0.08
In a cement silo windward area of the largest silo, the centre of gravity of the cement silo is also roughly in the middle of the silo body. The higher the force generated by the wind speed and the force generated by the earthquake acceleration from the ground plane, the greater the overturning force. Therefore, do not raise the cement silo barrel to shorten the length of the cement screw conveyor, which has certain unsafe factors.
Feel free to discuss the cement silo with us the technical.
If you have questions about the cement silo, want to know some theoretical knowledge about cement silo, or can give me some advice about cement silo, you are welcome to discuss it with us. Let's explore more about cement silos together.