Pneumatic conveying uses airflow energy to convey granular materials along the airflow direction in a closed pipe, a specific application of fluidization technology. The structure of a pneumatic conveying device is simple, easy to operate, can be used for the horizontal, vertical, or inclined direction of transportation in the process of conveying can also be carried out at the same time as the material heating, cooling, drying, and airflow classification and other physical operations or some chemical operations. In dry mortar production lines, pneumatic conveying is mainly used in the following aspects:
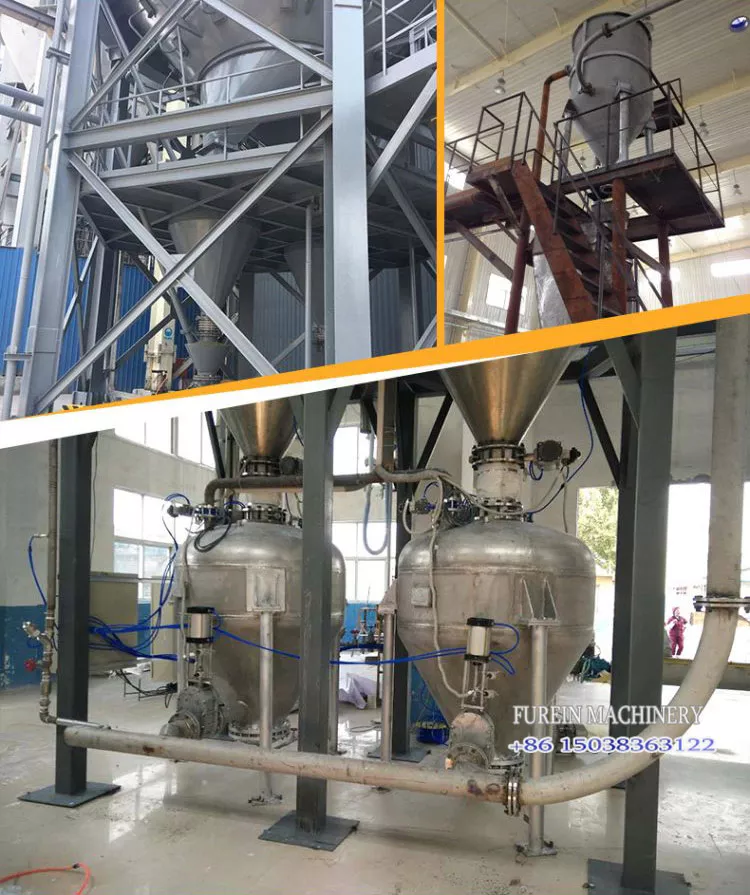
[lwptoc skipHeadingLevel="h1,h4,h5,h6"]
- Raw material conveying: pneumatic conveying can get raw materials such as cement, sand, fly ash, and so on from the storage silo to the batching machine. Pneumatic conveying has the advantages of long conveying distance, large transmitting capacity, and no environmental impact, which can effectively improve the utilization rate of raw materials and production efficiency.
- Additives conveying: pneumatic conveying can give additives, pigments, and other additives from the storage silo to the batching machine. Pneumatic conveying can ensure the additives are evenly mixed and improve product quality.
- Material mixing is used to mix two or more kinds of materials evenly.
- Material Classification: Materials are classified according to particle size.
- Finished Product Conveying: Pneumatic conveying can convey the finished mortar from the mixer to the packing machine. Pneumatic conveying can reduce manual operation and improve packing efficiency.
- Waste Material Conveying: It conveys waste materials from processing equipment to treatment equipment.
Pneumatic conveying system parts
The pneumatic conveying system is mainly composed of the following parts:
- Compressed air system: used to generate conveying airflow.
- Conveying pipe system: used for conveying materials.
- Pipeline valve system controls the airflow and material flow direction.
- Silo system: for storing materials.
Application of pneumatic conveying in dry mortar production line
In dry mix mortar production line, pneumatic conveying can transport the mortar quickly and evenly in the pipeline, significantly shortening the construction period and improving production efficiency. At the same time, the dry mortar positive pressure pneumatic conveying system can also realize accurate metering, avoiding the waste and loss caused by manual error.
In addition, with the cooperation of a screw conveyor, the metering system introduces the raw materials in the silo into the metering silo and realizes the raw materials' metering through the sensor's data feedback. The measured material is guided into the bucket elevator through the screw conveyor and lifted to the upper part of the mixer in the bin to be mixed. Waiting for the mixing bin for pneumatic large door type can quickly incorporate the materials into the gravity mixer to achieve continuous dry mortar production.
Advantages of pneumatic conveying in dry mortar production line
The application of pneumatic conveying in dry mortar production line has the following advantages:
- High conveying efficiency: pneumatic conveying can realize long-distance and large-volume sharing and improve production efficiency.
- Easy operation: The pneumatic conveying system has a simple structure, convenient operation, and easy maintenance.
- Cost saving: pneumatic conveying can reduce labor costs and lower production costs.
- Environmental protection: pneumatic conveying can reduce dust pollution.
Pneumatic conveying system shortcomings.
Pneumatic conveying is increasingly widely used in dry mortar production lines, an effective means to improve production efficiency and reduce production costs.
Of course, no such equipment or method is 100% perfect; pneumatic conveying also has its shortcomings, mainly including the following aspects:
- High equipment investment cost: pneumatic conveying system needs to be equipped with a compressed air system, conveying pipeline system, pipeline valve system, silo system, and other equipment; equipment investment cost is high.
- Dust pollution: certain materials in the process of pneumatic conveying will produce a small amount of dust pollution, and there is a need to take more stringent dust control measures; if there are higher environmental requirements, in the pollution port can be increased by dust removal equipment.
- Material separation: some materials are readily separated in the pneumatic conveying process, resulting in uneven mortar.
Solutions for pneumatic conveying shortcomings
Reduce the investment cost of pneumatic conveying.
Adopt advanced pneumatic conveying design technology:
- Adopting advanced design technology can improve the efficiency and performance of the equipment, thus reducing the investment cost of the equipment. For example, the use of new compressed air systems can improve air utilization and reduce compressed air consumption.
Adopt suitable equipment:
- According to the specific conveying needs, choosing the right equipment can reduce the investment cost of the equipment. For example, some people convey materials over short distances; low-pressure pneumatic conveying systems will reduce equipment investment costs.
Adopt energy-saving technology:
- Adopting energy-saving technology can reduce the operating cost of the equipment, thus reducing the overall investment cost of the equipment. For example, by adopting frequency conversion control technology, the flow rate and pressure of compressed air can be adjusted according to the actual demand, thus reducing the consumption of compressed air.
Reduce dust pollution
Adopt dense-phase conveying:
- Dense-phase conveying can reduce the friction between the material and the pipe wall, thus reducing dust generation.
Adoption of dust control device:
- Dust control devices can effectively collect and dispose of dust and reduce dust pollution. For example, cyclone separators, bag filters, and other equipment can collect and treat dust.
Strengthen management:
- Enhancing employees' safety awareness and dust prevention measures can reduce dust pollution.
Reduce material separation
Choose a suitable conveying method:
- According to the characteristics of the materials, choosing suitable conveying methods can reduce material separation. For example, for materials that are easy to separate, continuous conveying can be used to reduce the residence time of materials in the pipeline.
Optimize the conveying process:
- Optimizing the conveying process can reduce the vibration and collision of the material in the conveying process, thus reducing the separation of materials. For example, buffer devices can reduce pressure fluctuations in the conveying pipeline.
Adoption of grading devices:
- Classifying devices can classify materials into different particle size classes and reduce material separation.
The pneumatic conveying is applied in the dry mortar production line.
The picture below shows a customer in Russia using pneumatic conveying to transport raw materials and additives in a dry mortar production line. The conveying distance is 100 meters, and the conveying capacity is 100 tons/hour. The pneumatic conveying system consists of a compressed air system, conveying piping system, piping valve system, silo system, and so on. Through pneumatic conveying, the utilization rate of raw materials is increased by 20%, and the production efficiency is increased by 30%.
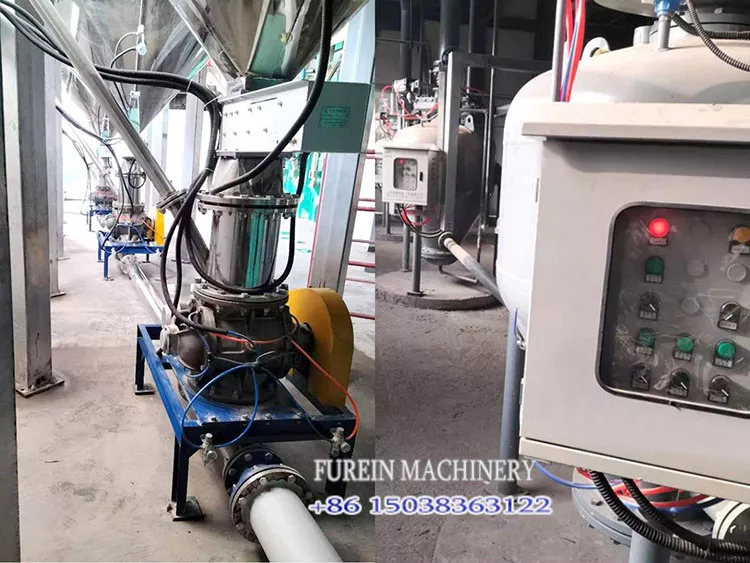