In a dry mix mortar plant, horizontal paddle and screw ribbon mixers are generally used. This dry mortar mixer is equipped with a hoist, which adopts a screw conveyor and is designed with a feeding port, which is convenient for feeding. During installation, the ground is generally excavated. The pit, the feeding port, is flush with the ground, which is suitable for feeding.
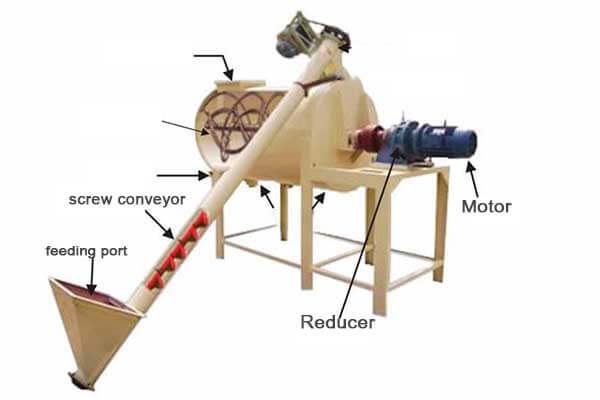
[lwptoc skipHeadingLevel="h1,h4,h5,h6"]
During the operation of the hoist, if there is material jamming in the falling bearing, this is reverse flow. If the hoist frequently flows backward, it will reduce the conveying capacity of the screw conveyor. For a screw conveyor with a large conveying capacity, the backflow material may also cause damage to the motor. Excessive current will generally burn the motor and cause a lot of economic losses.
In order to prevent this phenomenon from happening again, here are some methods:
First, check whether the motor is installed in the correct direction.
The screw conveyor equipped on the Furein mechanical dry mortar mixer is pasted with an arrow indicating the direction of rotation before leaving the factory. If the direction of rotation is incorrect, it is normal for the material to flow back on site. If the host does not have an arrow indicating the correct optional direction, it will likely be lost during long-distance transportation or use; please get in touch with the screw conveyor supplier in time.
Second, check whether there are any foreign objects between gears and bearings.
Foreign objects between gears and bearings, such as stone chips or steel scraps, will damage gear teeth or bearing bores and cause abnormal noise and vibration during operation. In addition to causing damage to gear teeth and bearings, they also lead to premature wear and tear of gear teeth or bearing bores. It is recommended that the objects should be removed at regular intervals according to actual needs.
Check whether the voltage is standard.
The voltage of the screw conveyor is 380V, 50HZ, or customized voltage. The lack of phase will cause the motor to be weak and unable to start, and it will cause damage to the engine for a long time, such as broken wires, lousy contact points in the electrical system, etc., so we need to check carefully whether there are signs of damage on them firstly.
Check whether there are foreign objects inside the bucket elevator.
Since the feeding port is located on the ground, it is easy to cause the entry of the ground items if you are not careful. In addition, for customers who use bagged raw materials, improper use will cause the woven bag to enter the bucket elevator, which will cause the elevator to block and reverse the flow of materials. In this case, it is necessary to Immediately stop the machine for inspection, remove foreign objects, and prevent the smell from being lost.
Check whether there is any damage in the material feeder or hopper.
If there is any damage in this part, it will also affect regular operation. For example, The material feeder has a hole on it, or its mesh screen breaks down; The hopper has cracks or gaps; The screw conveyor belt has cracks on it so that there is no power transmission function; The conveying screw shafts have broken off from their bearings due to overload; In addition, you should also check whether there are foreign objects such as nails or stones inside them.
Conclusion
How To Deal With Material Backflow During Screw Conveyor ConveyingThe special screw conveyor equipped with the dry mortar mixer is an integral part of the whole set of equipment. Inspection and maintenance to ensure the smooth progress of dry mortar mixing production. Regular maintenance will also prolong the service life of the equipment. Material backflow during screw conveyor conveying is a significant problem. The above methods can effectively eliminate the main reasons for the occurrence of this phenomenon and then further study why it occurs after stopping the main reasons. All in all, we hope that this article is helpful for your references. If none of the above answers solve your troubles, please contact us.